Forno alto
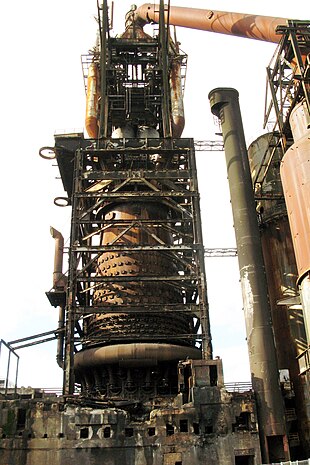

Um alto-forno (também desatualizado Hohofen ) é uma planta de grande escala com a qual o ferro-gusa líquido é produzido a partir de minérios de ferro processados (principalmente óxidos ) em um processo contínuo de redução e fundição .
Toda a planta também é conhecida como siderúrgica ou fundição e, além do alto-forno como componente central, possui outras instalações que garantem o funcionamento contínuo. Isso inclui o bunker para armazenar os materiais de entrada ( Möller : minério de ferro e agregados ) e os materiais de aquecimento ( coque ) com transporte conectado e sistemas de tubulação para trazê-los para a cabeça do forno na cabeça do forno. Outros dispositivos servem para descarregar o gás do forno na cabeça do forno, para fornecer o vento do soprador pré-aquecido pelo alto-forno na parte intermediária do alto-forno e para descarregar o ferro-gusa e a escória da base do forno.
Os aditivos contidos no Möller , tais como dióxido de silício (areia de quartzo) , o óxido de cálcio (cal) e outros, são utilizados durante o processo de alto-forno para ligar os constituintes indesejáveis do minério na escória e também baixar a temperatura de fusão da ferro . O coque aplicado em camadas serve como transportador de energia e agente redutor, e o vento quente soprado por várias ventaneiras fornece o oxigênio necessário .
Parte do carbono e a maior parte do fósforo e do enxofre que foram absorvidos devem então ser removidos do ferro-gusa produzido pelo refino antes que ele possa ser processado em vários tipos de ferro fundido ou aço . A escória e o gás de forno são produzidos como subprodutos . A escória é geralmente granulada e utilizada como escória na indústria de cimento. O gás de alto-forno é usado primeiro para gerar a explosão quente necessária e, em seguida, é usado como gás de aquecimento.
O processo de alto-forno moderno se desenvolveu ao longo de cerca de 5000 anos a partir de fogos de corrida simples ou fogos de lump alimentados com carvão e ventilados com ar frio em fornos de corrida e fornos de peça . O processo difere significativamente do alto-forno moderno. Os fornos clássicos usam redução direta para produzir ferro forjado sólido com baixo teor de carbono. Apenas a escória líquida escorre do forno. O ferro de corrida podia e então tinha que ser forjado para expulsar a escória presa. Em contraste com isso, o ferro-gusa produzido com o forno de jangada e subseqüente alto-forno, que foi aquecido com coque desde o início do século 18 e operado com uma explosão a quente desde 1828, deve ser descarbonetado em uma etapa de trabalho posterior.
A produção de uma tonelada de aço produz cerca de 1,37 tonelada de gás de efeito estufa CO 2 , grande parte do qual é produzida no processo de alto-forno. Na Alemanha, isso corresponde a cerca de um terço das emissões industriais. Portanto, muitas siderúrgicas de grande porte na Europa planejam substituir o processo de alto-forno por processos de baixa emissão, como a redução direta com hidrogênio , aproximando-se novamente do processo clássico.
história
Para o uso mais antigo e achados arqueológicos de ferro, veja
O início da fundição de ferro na Europa

Uma das primeiras formas simples e muito utilizadas de fundição de ferro foi o chamado fogo de corrida (também conhecido como Luppenfeuer ). Um poço em forma de funil com cerca de 30 centímetros de diâmetro foi preenchido com carvão e minério de ferro de turfa facilmente redutível , inflamado e abastecido com oxigênio de uma tigela hemisférica coberta de pele (uma forma inicial de fole ) que funciona como um leque . Após cerca de dez horas, havia um punho grande, preto, com grãos de minério de ferro e inalterado ou no solo prevalecia a escória Luppe ( ferro esponja acumulado). Durante a viagem da fornalha, o ferro não se liquefaz em uma fornalha de corrida. As temperaturas necessárias para isso podem ser atingidas sem problemas, mas o produto obtido desta forma seria fortemente carbonetado e não mais maleável. Durante a operação, a temperatura, portanto, tinha que ser mantida permanentemente em uma faixa que não permitisse que o metal se liquefasse. O forno de corrida , feito principalmente de argila ou pedras, foi um desenvolvimento posterior do fogo de corrida com uma abertura lateral para o suprimento de ar e um pequeno poço para encher e reabastecer com carvão antes e durante o forno. O poço também suportava o efeito de chaminé natural , de forma que temperaturas entre 1000 e 1200 ° C pudessem ser atingidas. O fornecimento de ar foi inicialmente realizado com uma tiragem natural, por exemplo, construindo sobre um aterro , e os fornos foram, portanto, denominados fornos de vento ou fornos de tiragem . No caso dos fornos ventiladores , entretanto, os foles proporcionavam um suprimento de ar mais eficaz e controlado. Dependendo da duração do ciclo do forno (4 a 20 horas) e dependendo do tamanho do forno, os primeiros ferreiros recebiam um trapo com um peso de alguns quilogramas a várias centenas de pesos . Este foi então liberado de carvão e escória por aquecimento repetido (pré-aquecimento) e forjamento , compactado e - principalmente usando produtos semi-acabados - processado nas peças de trabalho desejadas.
Veja também: Produção de ferro na área de Lahn-Dill e fundição de ferro entre os povos germânicos .
Os fornos de corrida com forjas acopladas, os chamados trabalhos de corrida, ainda eram comuns até o século XVIII. Eles empregavam cerca de cinco a dez homens e produziam cerca de 60 a 120 toneladas de bonecos por ano. 2,7 quilos de carvão foram queimados por quilo de ferro .
Desenvolvimento do alto-forno
Embora o forno de corrida tenha sido usado por muito tempo devido à sua construção simples, fornos mais potentes começaram a ser desenvolvidos já no início do século XIII. O forno de peças (também conhecido como "forno de lobo"), que recebeu o nome de um pedaço de ferro que foi retirado do forno, pode ser visto como um elo para o desenvolvimento dos altos-fornos de hoje . A fornalha era uma fornalha de tijolo quadrado de topo aberto , cujo tamanho cresceu de cerca de quatro metros de altura no final da Idade Média para dez metros de altura no século 17, como os fornos de peça em Vordernberg na Estíria , um centro de produção de ferro-gusa na Europa Central naquela época. Os foles dos fornos foram conduzidos por água rodas e os sistemas foram, por conseguinte, também referido como roda funciona . Eles atingiram temperaturas de até 1600 ° C; a mistura de minério de ferro e carvão foi parcialmente derretida. Um desenvolvimento posterior foi a fornalha azul, cujo nome foi derivado de uma corrupção da palavra inglesa sopro (= soprar). Em princípio corresponde ao forno à peça, mas tem a frente do forno fechada.
Na forja , porém, foi processado inicialmente apenas o ferro esponja (lóbulos) que se acumulou sobre o banho de ferro, que atingiu tal tamanho nos fornos de peça que não era mais processado manualmente, mas com martelos de forja também movidos a água. poder . O ferro-gusa fundido produzido pelo processo de fundição inicialmente parecia para as fundições como "ferro podre" que não podia ser usado porque havia absorvido uma proporção tão alta de carbono que era frágil demais para forjar. Chamava-se Saueisen na Alemanha e Graglach , fluxo de lama no Steiermark e ferro-gusa no mundo anglófono.
O problema só foi resolvido com a invenção de diversos processos de refino do ferro, por volta do século XIV. Isso também abriu o caminho para aumentar ainda mais a eficiência dos fornos. Os fornos de jangada eram construídos com alvenaria de vários metros de espessura, cuja estrutura era estreitada e na qual o ferro-gusa ( ferro - gusa e aço-carbono ) e a escória produzida após a conclusão do processo de fundição eram drenados juntos. Os fornos de jangada podem ser vistos como os "ancestrais" imediatos do alto-forno, uma vez que, em princípio, nada mudou no processo de extração do ferro após seu desenvolvimento. O forno de jangada mais antigo conhecido está no Kerspetal (Bergisches Land). É datado do ano 1275. Em Siegerland, havia cerca de 30 altos-fornos por volta de 1450. Com o aumento da eficiência dos fornos e a crescente demanda por hardware, porém, surgiu um novo problema: o carvão necessário para a geração de energia não podia mais ser atendido. Coal provisoriamente foi também ser usado, mas quase poderia apenas por Kohlengräberei em céu aberto ser vencida. Em 1755, havia quase 200 minas na área do Ruhr .
O inglês Abraham Darby I (1676–1717) finalmente teve sucesso em 1709 em Coalbrookdale na produção de ferro-gusa com a ajuda de coque , depois de algumas tentativas anteriores sem sucesso com carvão duro. Junto com a máquina a vapor que foi aprimorada por James Watt como uma unidade para o soprador, a eficiência dos altos-fornos poderia ser aumentada consideravelmente. Na Alemanha, no entanto, tentativas semelhantes foram inicialmente malsucedidas. Foi só em novembro de 1796 que a siderúrgica real em Gleiwitz conseguiu construir um alto-forno a coque funcional. Com a ajuda do coque, a quantidade de metal quente produzida poderia ser aumentada para até duas toneladas por dia, com um consumo de três toneladas e meia de coque por tonelada de ferro-gusa. Os ainda pequenos fornos frescos podiam processar apenas parcialmente essa quantidade de ferro-gusa ; o resto foi usado como ferro fundido .
Com o desenvolvimento das cúpulas no final do século XVIII, a indústria do ferro fundido viveu um verdadeiro apogeu. Em ferro fundido foram feitos canhões , sinos de igreja , utensílios de cozinha e, por fim, objetos de arte como fogões e fogueiras decoradas com relevos e até joias . Um dos maiores produtos de ferro fundido é a Ponte de Ferro na Inglaterra , construída em 1777/79, e a ponte de 12 metros construída em 1794 sobre o Striegauer Wasser perto de Laasan (agora Łażany ) no que hoje é a Polônia.
Uma melhoria final significativa no desempenho dos altos-fornos questionados quanto ao uso é o ar quente, que mais tarde passou a ser o alambique utilizado inicialmente pelos fogões tubulares (Neilson, 1828) e Cowper - foi entregue o fogareiro (1857).
Os primeiros altos-fornos conhecidos na Europa estavam na Suécia no século 13, por exemplo, em Lapphyttan . Altos-fornos individuais na França, Bélgica e, principalmente, Inglaterra foram identificados nos séculos seguintes. O alto-forno mais antigo e totalmente preservado da Alemanha é o Luisenhütte em Wocklum, perto de Balve, em Sauerland . Na Saxônia, três altos-fornos a carvão dos séculos 17 e 19 foram preservados em Brausenstein (1693), Schmalzgrube (1819) e Morgenröthe (1822). Um alto-forno de 1783 pode ser visto em Wilhelmshütte em Bornum am Harz e em Sauerland o Wendener Hütte, também construído no século 18, foi declarado um monumento técnico cultural. Na Turíngia , em Schmalkalden - Weidebrunn, funciona o novo museu do alto-forno Neue Hütte (Schmalkalden) . O alto-forno clássico tardio de 1835 mostra como o ferro-gusa era produzido a partir de minérios de ferro locais com base no carvão. A ferraria existiu até 1924.
Fundição de ferro fora da Europa
O forno Tatara , um tipo especial de forno de corrida usado no Japão para fazer ferro, é conhecido desde o século 7, no máximo . Em contraste com os fornos usados em outras regiões do mundo, um forno Tatara tem a forma de uma caixa com uma altura de cerca de 1,2 a 2 metros com uma largura superior de 0,8 a 1,2 metros, que se estende para baixo apenas a cerca de 0,5 metros. . O comprimento do forno, por outro lado, é de cerca de 4,5 metros. Em ambos os lados longos, 18 a 20 bocais de cerâmica garantem um suprimento de ar suficiente, que em empresas "modernas" é trazido por um ventilador acionado por vários homens. O forno Tatara é carregado alternadamente com carvão e areia de minério de ferro e atinge temperaturas de 1.200 a 1.500 ° C. Após cerca de três dias, as paredes do forno são quebradas e um bloco de ferro e aço maleável pesando cerca de duas toneladas é removido. A escória resultante foi previamente drenada durante a operação. Ainda hoje, o aço japonês ( tamahagane ) , tradicionalmente produzido nos fornos Tatara e conhecido por sua qualidade, é utilizado, por exemplo, para facas de cozinha de alta qualidade ( Hōchō ) ou para a katana de espada longa japonesa .
Os fornos chineses para fundição de ferro do século 19 assemelhavam-se a um cone truncado de cabeça para baixo com cerca de 2,5 metros de altura e um diâmetro superior de 1,2 metros, um diâmetro inferior de quase 60 centímetros e uma espessura de parede de 30 centímetros e eram feitos de argila . Como medida de segurança, o forno era cercado por uma cesta feita de malha de ferro e podia ser inclinada cerca de 30 ° para facilitar a remoção do ferro-gusa. Pedra de ferro marrom , pedra de ferro de carvão (“Blackband”) e, dependendo do tipo de construção, carvão ou coque foram cobrados. O ar necessário para reduzir o minério foi trazido por um soprador de cilindro manual . Dessa forma, poderiam ser produzidos entre 450 e 650 quilos de ferro-gusa por dia, com um consumo de coque de 100 quilos por 100 quilos de ferro. Uma instalação de alto-forno semelhante também foi encontrada na província de Bulacan , nas Filipinas , que funcionou até cerca de 1900. O alto-forno tinha a forma de um cone truncado de ponta-cabeça fechado na parte inferior com uma altura externa de 2,1 metros, um diâmetro externo na gota de 1,5 metros e uma espessura de parede entre 30 e 80 centímetros.
No início do século 20, foram descobertos povos na África que reduziam o minério de ferro com a ajuda de poços ou fornos de tração de um a três metros de altura. Para a construção, foram usados cupinzeiros, que foram devidamente escavados, ou a fornalha foi feita de argila. Vários bicos de cerâmica instalados na extremidade inferior do forno garantiam um suprimento de ar suficiente, que era sugado para cima através do minério e enchimento de carvão devido ao efeito de chaminé do poço alto. O minério e o carvão foram recarregados várias vezes pela abertura superior da chaminé, até que depois de cerca de 20 horas um pano do tamanho de uma bola de futebol foi criado, que foi removido por baixo através do peito quebrado da fornalha. O minério de ferro muito puro necessário para esses fornos veio de Banjéli em Bassariland , entre outros .
construção

Componentes da esquerda para a direita: Bunker, casa de guincho, linhas de gás de forno com saco de poeira atrás do elevador inclinado para carregamento, alto-forno, sala de drenagem, aquecedor de vento
A fim de garantir uma operação suave e contínua durante a chamada " jornada do forno " de 10 a 20 anos até a próxima data de manutenção , um sistema de alto-forno requer outras instalações essenciais além do próprio alto-forno. Isso inclui o bunker para os materiais de entrada com um sistema de transporte conectado para carregamento contínuo do alto-forno, com o qual os materiais de entrada são colocados no forno através da escotilha superior . O ar , que foi pré-aquecido no aquecedor de explosão , é soprado para o alto-forno através de bicos através de um tubo de anel de vento quente , que é forrado com um revestimento interno à prova de fogo e cercado por um sistema de resfriamento complexo do lado de fora . Conectado ao alto-forno está um corredor de vazamento ou vazamento especialmente desenvolvido , no qual o ferro-gusa removido pode ser alimentado em conchas ou vagões de torpedo apropriados durante o vazamento regular e transportado para processamento posterior.
A construção de uma planta de alto-forno moderno é um projeto extenso de grande escala de uma usina siderúrgica e leva entre 1,5 e 2,5 anos do planejamento ao comissionamento, dos quais o trabalho de planejamento leva cerca de metade do tempo. Os custos de investimento para a construção do novo "Alto Forno 8" em Duisburg-Hamborn, por exemplo, ascenderam a cerca de 250 milhões de euros.
bunker
Os materiais de entrada, como minérios de ferro, coque e agregados (por exemplo , cal , areia e dolomita ), que geralmente são entregues por ferrovia ou navio, são primeiro trazidos para um bunker. Consiste em vários bunkers , que são feitos de tijolos ou fundidos em concreto armado e nos quais as matérias-primas que chegam são armazenadas. Para compensar as diferenças de qualidade na composição de Möller (minério de ferro, agregados) e coque, os materiais são frequentemente misturados de antemão nos chamados leitos mistos .
Algumas matérias-primas já são preparadas pelos fornecedores (inclusive minas ). Em alguns casos, uma preparação a montante, por exemplo, em uma britagem de minério, sinterização e planta de pelotização , deve garantir o processamento, uma vez que o tamanho da partícula ou do grão das matérias-primas não deve ser muito pequeno (risco de entupimento, fluxo de gás pobre) nem muito grande (não é a utilização ideal da matéria-prima).
alimentação
Möller e coque são transportados do bunker para a extremidade superior do poço, a chamada gota . O fornecimento do material também é denominado carregamento ou carregamento e, dependendo do espaço disponível, ocorre por meio de correias transportadoras , caçambas de despejo ou pequenos vagões a granel , os chamados caminhões ou hunte (também cães ).
No caso de carregamento de vagões ou “pular carregamento”, o carregamento ocorre por meio de um elevador inclinado até a abertura de enchimento chamada “top hatch”, que forma a extremidade superior do alto-forno. Dois sistemas de elevador são usados para cada alto-forno, que transportam alternadamente coque e Möller. Além da maior capacidade de abastecimento, a utilização de dois elevadores também serve como proteção contra falhas de forma a garantir o abastecimento ininterrupto do alto-forno. As correias transportadoras são agora preferidas para carregamento em altos-fornos modernos. Embora eles só possam superar pequenos gradientes e exigir mais espaço, eles são mais eficientes, mais fáceis de automatizar e manusear o material a granel com mais cuidado.
Oclusão de gota
O gás do forno que sai pela cabeça do forno consiste principalmente de nitrogênio quente (N 2 ), monóxido de carbono (CO) e dióxido de carbono (CO 2 ), bem como pequenas quantidades de outros gases e poeira arrastada (ver também produtos de alto forno ) . Apesar da periculosidade dessa mistura de gases tóxicos e inflamáveis, a abertura de gota permaneceu destrancada por muito tempo. Somente a partir do desenvolvimento do fogão a gás de alto-forno, no século XIX, foi adicionado um sistema de bloqueio, que possibilitou carregar o alto-forno sem perder o combustível e o gás de aquecimento agora valiosos. O gás da fornalha é interceptado por meio de grandes canos, retirado da poeira e enviado aos queimadores da caldeira, entre outras coisas .
O primeiro selo de gota com uma fechadura de funil simples foi inventado por George Parry em Ebbw Vale em 1850 , que mais tarde ficou conhecido como "funil de Parry". A forma mais difundida de eclusa superior até a década de 1970, entretanto, era a “fechadura de sino duplo” com um funil giratório desenvolvido por McKee e interposto para distribuir o material a granel. No entanto, sistemas com três ou quatro sinos também foram utilizados para reduzir a altura de despejo, o que pode comprometer o diâmetro definido das pelotas de minério e, no caso de altos-fornos com contrapressão mais elevada, o forno. O grande peso desta construção e os crescentes problemas em manter a estanqueidade do sistema de campânula acabaram por limitar os esforços para aumentar o desempenho dos altos-fornos com fechaduras de sino.
A invenção da empresa luxemburguesa Paul Wurth SA, nomeadamente Édouard Legille , que em 1970/1971 desenvolveu o chamado "selo de gota sem sino" (mais tarde também "selo de gota Paul Wurth") trouxe uma melhoria significativa no selo de gota . Em vez de um sistema de sino complexo e pesado, dependendo do tamanho e das necessidades do alto-forno, agora existem dois ou mais tanques de armazenamento de coque e Möller na cabeça do forno, que são preenchidos com vagões a granel por meio de distribuidores de correia ou sistemas de elevadores. A Coca e o Möller passam por tubos de queda no meio do fechamento do forno para uma calha giratória e giratória , que pode distribuir o material que entra de maneira precisa e uniforme na superfície de vazamento. O sistema é selado por abas de vedação localizadas acima e abaixo dos recipientes de armazenamento. Uma aba de material adicional sob os recipientes garante uma velocidade de descarga constante do material a granel. A altura total da nova “vedação de gota sem sino” foi reduzida em cerca de 1/3, o que também reduziu o peso da construção, e a estanqueidade do sistema foi mais fácil de garantir.
Em 9 de janeiro de 1972, a primeira escotilha superior sem sino do mundo foi colocada em operação no alto-forno 4 da siderúrgica August Thyssen em Hamborn . Devido às muitas vantagens sobre o sistema antigo, a rolha de gota Paul Wurth sem sino estabeleceu-se com sucesso e é preferida para uso em sistemas modernos de alto-forno.
Forno alto
Projeto
O próprio forno assemelha-se a um princípio de forno de poço , uma lareira ou chaminé , visto que estes formam a base do efeito de chaminé resultante facilita a gaseificação ideal da alimentação. A altura do núcleo do alto-forno determina seu desempenho e pode estar entre 30 e 75 m. Os 3/5 superiores formam o eixo real, que corresponde a um cone truncado alongado. Isso é seguido por um curto anel intermediário cilíndrico com o maior diâmetro interno no alto-forno, que é conhecido como "saco de carvão". Outro cone truncado de cabeça para baixo, o chamado “Rast”, finalmente termina na “estrutura” inferior, de desenho cilíndrico. O saco de carvão e o Rast, bem como a estrutura, cada um perfaz 1/5 da altura total. Com uma altura total de 30 m, o fuste tem cerca de 18 m, o saco de carvão e Rast cerca de 6 m e a moldura também 6 m.
Toda a construção do alto-forno é tipicamente cercada por uma estrutura de aço com plataformas de trabalho e montagem, que por um lado serve para acomodar o equipamento auxiliar, como o elevador de material e, se necessário, a escotilha superior, mas também pode ser usada para apoiar e estabilizar o alto-forno. Uma distinção pode ser feita entre dois tipos de estrutura de suporte:
Os altos-fornos mais antigos e predominantemente americanos são equipados com um anel de suporte com pilares de suporte aproximadamente no nível do resto, por meio do qual a carga que se encontra no alto-forno da cabeça do forno e da eclusa superior é conduzida para a fundação. As colunas de suporte, no entanto, resultam em uma constrição e, portanto, uma obstrução do acesso à área de vazamento, bem como problemas na área de conexão entre o trinco e o anel de suporte. Por causa dessas desvantagens, a segunda variante agora é preferida para altos-fornos mais novos.
Este projeto, desenvolvido na Alemanha, é o chamado “alto-forno autônomo”. A blindagem de aço do alto-forno cria uma estrutura de forno autoportante, que é circundada por andaimes completos para plataformas de trabalho e para acomodação dos equipamentos auxiliares. Isso significa que não há colunas irritantes na área de vazamento e o alto-forno pode seguir livremente todas as expansões térmicas que um compensador conectado à cabeça do forno absorve.
A altura total de tal planta é de cerca de 90 m. O alto-forno 2 em Duisburg-Schwelgern, por exemplo, tem uma altura de forno de quase 75 m, um diâmetro de moldura de 14,9 m e um volume útil de cerca de 4800 m³, derrete cerca de 12.000 t de ferro-gusa por dia e está atualmente em vigor (em 2014) como o maior alto-forno da Europa. Doze altos-fornos no mundo excedem o volume útil de 5.500 m³ (em 2013). O maior alto-forno conhecido no mundo até hoje, com um volume útil de 6.000 m³, está localizado na " Gwangyang Steel Works" da POSCO, na província sul-coreana de Jeollanam-do.
Na extremidade inferior do batente está a abertura de rosca para o ferro-gusa, fechada com um tampão de cerâmica, por onde podem ser drenados os produtos metalúrgicos resultantes do ferro-gusa e da escória. Para o esvaziamento completo ("Sauabstich"), quando o revestimento do alto-forno for iminente, um "Sauloch" (também porca de forno ) é fixado no ponto mais baixo da estrutura, bem como em seu fundo .
Os bicos da linha do anel de vento quente são posicionados na fronteira entre o resto e a estrutura e são alimentados por aquecedores de ar quente.
![]() |
Região e período | Frame Ø d em m |
Altura H em m |
Volume utilizável em m³ |
Produção em toneladas por dia |
---|---|---|---|---|---|
1) Alto-forno 1861 | 0.9 | 15,3 | 64 | Dia 25 | |
2) Alto-fornos especiais de ferro-gusa da Alemanha Ocidental da década de 1930 | 4,5 | 20,0 | 425 | 450 | |
3) Alto-fornos de aço da Alemanha Ocidental e ferro-gusa Thomas 1961 | 6,5 | 24,0 | 900 | 1.200 | |
4) Altos-fornos da Alemanha Ocidental 1959 | 9,0 | 26,1 | 1.424 | > 2.000 | |
5) Altos-fornos soviéticos 1960 | 9,8 | 29,4 | 1.763 | 4.000 | |
6) Altos-fornos japoneses 1968 | 11,2 | 31,5 | 2.255 | 6.000 | |
7) Grandes altos-fornos da Alemanha Ocidental 1971/72 | 14,0 | 36,7 | 4.100 | ≈ 10.000 |
Forro de tijolo
Originalmente, os altos-fornos consistiam em uma alvenaria de suporte de carga e isolante de calor de um metro de espessura, feita de tijolos ou entulho (paredes de fumaça) e tinham um revestimento refratário na parte interna ( paredes do núcleo) . Nos altos-fornos modernos, a armadura de aço com centímetros de espessura e a estrutura de suporte assumem a carga, enquanto a alvenaria do núcleo sozinha fornece a resistência ao fogo e o isolamento térmico necessários.
A fim de alcançar a vida útil desejada (curso do forno) até que a renovação completa do revestimento do forno seja devida, todo o núcleo do forno, desde o eixo até a estrutura, é refratário . O revestimento do forno também define o perfil interno final do forno. Com uma área total de cerca de 2.000 m² e uma espessura de alguns decímetros a mais de um metro, a alvenaria de grandes dimensões pode gerar custos enormes, razão pela qual, na fase de planejamento, os esforços são feitos para usar apenas pedras especialmente adaptadas para os requisitos da respectiva seção do forno.
Na parte superior do eixo, as temperaturas são relativamente baixas, mas as tensões mecânicas são altas devido ao impacto do carregamento. Consequentemente, chamotas com um conteúdo de corindo entre 30 e 40% são usadas aqui. Além disso, uma “armadura de impacto” feita de placas de aço é fixada na área de alimentação para evitar danos à alvenaria causados pelo impacto dos materiais de argamassa.
Na área do poço inferior até o saco de carvão, as temperaturas aumentam rapidamente. O estresse causado pela abrasão só diminui lentamente, entretanto, uma vez que a carga deve permanecer firme pelo maior tempo possível e suportar a pressão da coluna de Möll para permitir um bom fluxo de gás. Além disso, as pedras nesta área devem ser quimicamente estáveis, à medida que aumenta a reatividade das substâncias circundantes. Consequentemente, chamotas altamente refratárias com um conteúdo de corindo entre 60 e 86% ou tijolos de semigrafite são usados aqui.
Ao nível dos tuyeres e da área de captura que reveste as mais altas temperaturas e pressões está exposto, que apenas os tijolos de carbono , Schmelzspinellsteine com cromo ou Chromkorundsteine suportam.
resfriamento
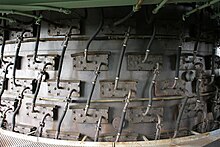
Para proteger contra superaquecimento, o alto-forno contém um sistema de linhas de água de resfriamento e elementos (aduelas) que são conectados à armadura desde cerca do terço superior do eixo até a base da estrutura . Como um alto-forno com diâmetro de moldura de 8 m tem um movimento de água de mais de 30.000 m³ por dia, o que corresponde ao consumo de uma cidade de médio porte com cerca de 200.000 habitantes, o sistema de refrigeração deve ser projetado de acordo e protegido várias vezes para proteger contra falhas.
Nos altos-fornos modernos do século 20, os circuitos de resfriamento abertos anteriormente difundidos são usados principalmente para a cabeça do forno e irrigação de rack e em emergências (por exemplo, se um circuito fechado falhar). Em circuitos abertos, a água necessária é retirada dos corpos d'água próximos (rios, lagos) e limpa de sólidos antes de ser usada no sistema de resfriamento. Após o uso, as torres de resfriamento assumem o resfriamento da água antes que ela seja devolvida ao ambiente. Os circuitos fechados, por outro lado, usam água tratada, dessalinizada e desgaseificada, que é resfriada novamente após o uso por meio de um trocador de calor e, em seguida, retorna ao sistema de refrigeração. Além de proteger os elementos e linhas de resfriamento de depósitos, a água tratada tem a vantagem de que o sistema de resfriamento pode absorver maiores quantidades de calor.
A construção dos elementos de refrigeração é concebida de forma que, por um lado, possam suportar a alvenaria, mas, por outro lado, também podem ser substituídos rapidamente se estiverem danificados. Eles consistem em chapa de aço, ferro fundido ou cobre e são aparafusados, cunhados ou soldados à armadura. Quando se trata do design dos elementos de resfriamento, uma distinção pode ser feita entre dois tipos básicos:
- As caixas de resfriamento são elementos retangulares planos com placas-guia desenhadas como um labirinto para direcionar o fluxo de água e um perfil que se estreita em direção ao meio do forno, o que permite uma rápida remoção e instalação. As caixas de resfriamento são inseridas entre as placas de armadura do eixo, de modo que um padrão semelhante a um tabuleiro de xadrez de placas de armadura e caixas de resfriamento é criado.
- Os resfriadores de placa ou aduelas são feitos de fundição especial com tubos de resfriamento verticais fundidos. Eles são aparafusados ao lado da armadura voltado para o centro da fornalha. A superfície de apoio das aduelas é entrecruzada por ranhuras preenchidas com massa isolante.
Diferentes tipos de resfriamento são usados no alto-forno, dependendo dos requisitos de capacidade de resfriamento. A cabeça do forno é resfriada na área da armadura de impacto com um sistema de sprinklers externo. A maioria das caixas de resfriamento são instaladas na área do poço e as caixas de resfriamento e resfriadores de placas são usadas na área de Kohlsack e Rast. Devido à carga de calor particularmente alta nesta área, os elementos de resfriamento são colocados em intervalos próximos para que tanto calor quanto possível possa ser dissipado. Os moldes de sopro têm seu próprio circuito duplo de resfriamento. A estrutura e a base são resfriadas com água corrente ou pela introdução de água em uma camisa de estrutura dupla.
Fogão de explosão
James Beaumont Neilson foi um dos primeiros a explodir fogões em design recuperativo - o ar exigido pelo trocador de calor aquecido - desenvolvido e patenteado à esquerda. Anteriormente, os altos-fornos eram sempre operados com ar frio, pois a indústria metalúrgica há muito experimentou que um alto-forno funcionava melhor no inverno do que no verão. Portanto, Neilsen inicialmente encontrou grande oposição ao tentar usar o novo princípio. Os trabalhadores também não foram convencidos por um experimento com um vento soprador, permitido pela Clyde Iron Works em 1828 , que só foi aquecido a 27 ° C e ainda garantiu que a escória produzida fosse menos ferro e significativamente mais fluida. O aquecedor de explosão de construção simples de Neilson consistia em um pedaço de linha de alimentação dobrada em forma de abóbada, que era aquecida em uma lareira . Uma caixa de chapa metálica montada sobre a abóbada do tubo reteve o calor por um tempo para melhorar a transferência de calor. Outras melhorias estruturais através do uso de tubos e caixas de ferro fundido mais resistentes ao calor, bem como bobinas de aquecimento alongadas e curvas para absorver a expansão térmica permitiram que esses "aquecedores de vento tubulares" aquecessem o vento do soprador até 315 ° C.
ano | Sistema de vento | Consumo de combustível em kg por t de ferro-gusa |
Quantidade de ferro-gusa em 24 horas em kg |
1829 | Vento frio | Coca 8060 | 1607 |
1830 | Vento quente | Coca 5160 | 2353 |
1833 | Vento quente | Carvão bruto 2280 | 3556 |
A resistência ao uso da explosão a quente diminuiu completamente à medida que os lucros do ferro-gusa aumentavam cada vez mais e, ao mesmo tempo, a quantidade de combustível necessária podia ser reduzida consideravelmente. Até o carvão bruto agora podia ser usado, o que antes era impossível.
O gás de alto forno também é usado na metalurgia desde meados do século XVIII, mas inicialmente apenas para torrefação de minério, secagem de moldes de fundição e queima de cal e tijolos. Não foi até Wilhelm von Faber du Faur, que conseguiu desenvolver um aquecedor tubular eficaz e estável, o "Wasseralfinger Winderhitzer", que foi aquecido com gás de alto forno e elevou a temperatura do vento para 540 ° C. No entanto, isso também significa que o limite de desempenho deste design foi atingido.
Uma melhoria decisiva no fornecimento de altos-fornos com explosão a quente foi finalmente alcançada por Edward Alfred Cowper (1819–1893), não mais construindo o aquecedor de explosão a partir de um sistema de tubos, mas com tijolos multi-perfurados refratários permeáveis ao ar . Ainda na primeira fase de desenvolvimento, os “aquecedores de vento Cowper” levaram 29 m³ de ar a uma temperatura de 650 a 700 ° C em um minuto. Naquela época, a temperatura do vento só podia ser medida com amostras derretidas de diferentes metais. As amostras usadas anteriormente feitas de chumbo ( SP = 327,4 ° C) e zinco (SP = 419,5 ° C) não podiam mais ser usadas nos aquecedores de Cowper e até mesmo o antimônio (SP = 630,6 ° C) derreteu em segundos. Outra inovação, também desenvolvida por Cowper, foi a alternância regenerativa de dois aquecedores eólicos, em que um era aquecido por queima de gás de forno, enquanto o outro liberava o calor armazenado para o ar frio soprado.
O “Cowper-Windheater” mais moderno consiste em um tubo de aço vertical de 20 a 35 m de altura e 6 a 9 m de diâmetro. O núcleo consiste inteiramente em tijolos de sílica com múltiplos furos empilhados . Em um lado do poço, um poço de combustão revestido à prova de fogo é dividido até o nível da cúpula, que ocupa cerca de um terço da seção transversal do aquecedor. Os bicos do queimador e as conexões para ar frio e ar quente estão localizados no eixo de queima inferior. Outra possibilidade é a construção de um eixo de combustão que fique localizado na parte externa, independente do eixo do aquecedor. Este projeto tem a vantagem de que, por um lado, as fissuras que ocorrem na parede divisória entre os eixos de combustão e aquecimento devido às fortes oscilações de temperatura são evitadas e, por outro lado, o próprio aquecedor tem mais espaço para multi-perfurações pedras e, assim, a potência de aquecimento pode ser aumentada novamente.
Normalmente três e, no caso de altos-fornos maiores, quatro “cowpers” garantem um suprimento suave e sem problemas de ar quente para o alto-forno. Enquanto dois são aquecidos em momentos diferentes, um ventilador axial ou radial empurra o ar frio (cerca de 1,4 t por tonelada de ferro-gusa) através do terceiro aquecedor a uma pressão de 2 a 4,5 bar. Os sopradores de pistão a vapor ou gás usados anteriormente provaram ser antieconômicos e difíceis de controlar. Em um ciclo contínuo, ocorre a mudança para o cowper previamente aquecido, enquanto o cowper resfriado é aquecido novamente. A fase de aquecimento leva cerca de 50 minutos, a fase do vento, no entanto, apenas cerca de 30 minutos, uma vez que o termoacumulador não deve cair abaixo da temperatura de 721 ° C, que é crítica para os tijolos de sílica. Abaixo dessa temperatura, os tijolos de sílica sofrem várias alterações de modificação , o que leva a um "salto de volume" que destrói a estrutura sólida da guarnição de tijolo multi-perfurada e pode causar seu colapso. O terceiro ou quarto “cowper” também serve como reserva contra falhas e durante o trabalho de manutenção.
Linha de anel de vento quente e bicos


Com uma temperatura máxima atingível de 1270 ° C (1980) a 1350 ° C (1985), a explosão quente chega através da "linha de anel de explosão quente" para entre 10 e 40 bicos, dependendo do tamanho do alto-forno, e através dos chamados moldes de sopro no forno. Para reduzir o consumo de coque, agentes redutores substitutos, como gordura animal ou óleo de aquecimento pesado, são injetados nos moldes de muitas fábricas. No entanto, como o preço do petróleo continuou a subir ao longo do tempo, houve várias tentativas com outros substitutos.
Na Armco, nos EUA , o pó de carvão foi usado com sucesso como substituto do combustível por períodos mais longos e nas fábricas chinesas a partir de 1963, mesmo em operação contínua. Desde 2006, também foram adicionados plásticos antigos finamente peletizados (6 mm × 9 mm), que além da reciclagem ecológica dos resíduos plásticos , ao contrário dos aterros, também reduzem a emissão de CO 2 e SO 2 .
Para proteger contra os danos causados pela carga de calor, a linha do anel e a conexão de alimentação são fornecidas com um forro à prova de fogo, que também tem um efeito de isolamento térmico para evitar perdas de calor. Os próprios moldes de sopro são resfriados intensamente com água porque, dependendo do grau de desgaste do revestimento do forno, eles podem se projetar até meio metro para dentro do forno e, então, são expostos aos maiores esforços devido à temperatura e pressão de a coluna Möll. Nos altos-fornos modernos, portanto, apenas as formas ocas feitas de cobre eletrolítico com um circuito de água de resfriamento de câmara dupla são usadas. Se a câmara frontal queimar durante a viagem do forno, o circuito de resfriamento correspondente pode ser desligado e a câmara principal pode ser continuada até a próxima paralisação.
Furação de ferro-gusa e escória

O ferro-gusa - trasfega em intervalos regulares de cerca de duas a três horas. Aqui, a ficha de cerâmica para o buraco da torneira é com ar comprimido - broca perfurou. Em casos raros, por exemplo, se a broca falhar, a abertura também é perfurada com uma lança de oxigênio .
O ferro-gusa então flui por cerca de 15 a 20 minutos em uma área de vazamento ou vazamento especialmente desenvolvida com uma plataforma de trabalho e um sistema de canal de tijolo à prova de fogo, que é adicionalmente estampado ou derramado com compostos refratários. Em altos-fornos mais antigos, com maior produção de escória, parte da escória era primeiro extraída como a chamada "pré- escória " no nível da plataforma do molde. Em seguida, o ferro-gusa e a escória eram batidos juntos usando uma espécie de sifão, o chamado " raposa ", que separava a escória do ferro-gusa (como decantação ) e a desviava em diferentes direções por meio de um sistema de canal projetado de forma correspondente. Altos-fornos modernos com menor produção de escória, mas com uma produção diária de ferro-gusa de 3.000 toneladas e mais, não precisam de nenhum pré-vazamento da escória, mas entre dois e quatro furos. O sistema de sarjetas e raposas é correspondentemente complexo e requer monitoramento cuidadoso.
No canal principal entre a torneira e a raposa, que tem cerca de 8 a 14 metros de comprimento e comporta cerca de 20 a 60 toneladas de ferro-gusa incluindo a escória, a escória tem tempo de se separar do ferro-gusa e se acumular na superfície. Na frente da raposa, cujo “nariz” mergulha no banho, a escória se acumula e é drenada por canais que se ramificam para os lados. O ferro-gusa, por outro lado, flui sob a raposa através de um orifício sob o qual uma concha ou vagão torpedo está pronto para transportar o ferro capturado para processamento posterior na aciaria ou fundição . A escória também é coletada em vagões especiais e transportada para processamento posterior.
Após a conclusão da fase de rosqueamento, o orifício é fechado novamente com a ajuda de uma "máquina de socar orifício" até a próxima torneira.
As salas de fundição modernas devem ser "limpas" para proteger os funcionários e o meio ambiente, o que significa que os sistemas de sucção são instalados na área dos furos e no ponto de transferência para os recipientes de coleta e o sistema de canal é coberto com aço pratos. Os gases de exaustão capturados são limpos em sistemas de filtros apropriados .
função
Soprar
Antes que um novo alto-forno possa entrar em produção, ele deve primeiro ser seco lentamente com a ajuda de queimadores de gás ou soprando ar quente. Só então ocorre o verdadeiro “sopro” no forno. A escolha do método de sopro tem um grande impacto em seu modo de operação subsequente e em sua vida útil, pode variar de planta para planta e leva cerca de uma a duas semanas (com altos-fornos mais antigos às vezes até vários meses).
Após a secagem, a moldura é preenchida com madeira e coque pela primeira vez. No poço acima, camadas de coque e moler consistindo de minério de ferro e agregados de ligação de escória são despejadas, acesas e ventiladas por sopro de ar quente. A composição da estratificação expandida é muito diferente da estratificação operacional posterior. Ele contém muito mais coque, pois o aquecimento do forro do forno e a coluna de coque-Möller frio consomem muita energia. O uso de uma quantidade correspondentemente alta de escória garante que o quadro seja aquecido e protegido.
Estrutura e comportamento do carregamento durante a passagem do forno
A forma, composição e propriedades mecânicas da alimentação, especialmente dos minérios, bem como uma granulometria o mais uniforme possível, são de importância decisiva para a eficiência de um alto-forno . O comportamento de redução a temperatura elevada também desempenha um papel, o objetivo é conseguir uma quebra de temperatura tão baixa quanto possível e uma temperatura de amolecimento alta com uma faixa de temperatura baixa simultânea da fase de amolecimento. Somente se o sinter e os pellets permanecerem fragmentados e no estado sólido pelo maior tempo possível, eles poderão suportar a carga de pressão das camadas superiores e garantir uma boa penetração do gás.
O reducibilidade da sinterização depende da sua composição e é determinada pelo empírica tamanho da basicidade
que mostra a proporção de massa de óxido de cálcio e óxido de magnésio para dióxido de silício . A redutibilidade é melhor se a basicidade da composição estiver na faixa básica (B> 1,0) e atingir uma redutibilidade máxima na faixa de 2,0 a 2,5. A resistência mecânica também é maior nesta área. A partir de uma basicidade igual ou superior a 2,6, aumenta a proporção da fase fundida na porção sinterizada, o que fecha os poros e reduz a capacidade de redução, uma vez que os gases redutores não atingem mais a porção do minério diretamente. No caso da sinterização ácida (B <1,0), a fase de amolecimento começa em alguns casos quando apenas cerca de 15% do minério foi reduzido.
Em contraste com o sinter, os pellets tendem a ter uma composição ácida, porque sua forma esférica estável significa que há menos tendência para a formação de grãos finos e deterioração das propriedades mecânicas. Os peletes, portanto, consistem principalmente de hematita , vários silicatos para ligar a escória e os poros. A proporção de hematita deve, no entanto, permanecer limitada, pois, caso contrário, a estrutura dos pellets se afrouxaria muito no curso da redução e os pellets acabariam se desintegrando em pó concentrado, o que resultaria em uma perda considerável de resistência à compressão. O aumento excessivo simultâneo no volume da pelota (limiares) também acarreta o risco de entupimento do alto-forno.
A fim de saber como a estrutura e a condição do carregamento mudam no trajeto do forno até a abertura do macho e quais reações ocorrem na respectiva seção do forno, diversos testes foram realizados na década de 1970, principalmente no Japão, nos quais os altos-fornos foram parados no meio da produção e resfriados intensamente com água. Todas as reações em andamento dentro da Möllersäule foram, portanto, “congeladas”, por assim dizer. As análises subsequentes da composição da camada em diferentes níveis mostraram que a zona de amolecimento e fusão se projeta para cima em forma de sino no eixo central. O centro do sino consiste em coque, que ainda é permeável aos gases na zona quente de 1000 a 1600 ° C. Os minérios de fusão e a escória atingem o interior por meio desse sino de coque ativo e afundam no resto e na estrutura, enquanto a explosão quente que é soprada é distribuída uniformemente para fora e para cima. O chamado “homem morto” assumido até agora - um corpo em forma de cone em repouso e sem resposta feito de coque e ferro solidificado - não existe.
Apenas o pé desta “zona coesiva” é impermeável ao gás e está idealmente localizado ao nível do resto. Também não deve ser afetado pela gaseificação, de modo que, por um lado, a liberação (revestimento refratário) do saco de carvão e o resto são menos afetados e, por outro lado, a turbulência resultante do vento quente faria um redução uniforme do carregamento mais difícil ou mesmo impedi-lo. A fim de otimizar o fluxo de gás na forma descrita e, assim, reduzir o consumo de energia e ao mesmo tempo aumentar a qualidade do ferro-gusa, um cálculo cuidadoso das seções transversais da zona, bem como a quantidade e composição do quente a explosão introduzida é de grande importância.
As seguintes conclusões adicionais foram obtidas a partir da investigação em altos-fornos "congelados":
- A carga alternada de Möller e Coca é mantida ao longo de todo o forno até as camadas mais profundas. Apenas as espessuras da camada tornam-se menores no decorrer da redução.
- Ao nível do plano de sopro, ao invés do minério sólido, existem apenas gotas de ferro metálico e coque misturado à escória.
- A redução começa 3 a 4 metros abaixo do nível de carregamento, fazendo com que o tamanho do grão do sínter, pelotas e granulado diminua uniformemente. O sinter se decompõe a uma temperatura de 200 a 500 ° C, enquanto a do minério granulado ocorre apenas em torno de 800 a 900 ° C.
- 7 metros abaixo da superfície, a redução progrediu tanto que a porção de sinterização não se decompõe mais. No entanto, isso não se aplica ao outro Möllerstoff, uma vez que até uma profundidade de 18 metros, uma proporção cada vez maior de grãos finos abaixo de 5 milímetros foi encontrada. Se e em que ponto o grão fino é formado no alto-forno depende, no entanto, da temperatura e da distribuição do fluxo de gás, da taxa de aquecimento e do tipo de carga. No caso de sinterização, a proporção de grãos finos é geralmente maior.
- A redução ocorre muito mais rápido no meio da seção transversal do forno do que na área da borda.
- No auge da gota, a firmeza de todas as substâncias no óleo inicialmente diminui drasticamente e aumenta novamente com o aumento da profundidade, o que está relacionado à progressão da redução e ao aumento associado no teor de ferro.
Redução de enxofre de pragas
Os álcalis e os compostos de enxofre sempre presentes na alimentação têm grande influência nos processos de redução . Os compostos de enxofre, em particular, têm um efeito particularmente desvantajoso nos processos de redução que estão ocorrendo, uma vez que eles nunca podem ser eliminados completamente, apesar do pré-tratamento complexo de minério e coque. Mesmo pequenas quantidades de dióxido de enxofre (SO 2 ) de cerca de 5 a 50 ppm no gás redutor inicialmente aceleram consideravelmente a decomposição do oxigênio; No entanto, assim que o primeiro ferro metálico aparece, o processo é revertido e a decomposição do oxigênio é bastante desacelerada. A causa dessa reação é a propriedade do enxofre de se combinar com o ferro metálico na superfície e, assim, evitar a absorção de carbono.
A reação da wüstita (óxido de ferro (II), FeO) com o monóxido de carbono (CO) geralmente ocorre não apenas sobre a superfície do FeO, mas também sobre a superfície do ferro que já se precipitou. Devido ao melhor comportamento de absorção do ferro, grande parte do transporte de gás de e para o limite da fase ferro-óxido ocorre através do mesmo . No entanto, isso só acontece quando o ferro é capaz de absorver (cementar) carbono suficiente. Se a absorção do carbono for bloqueada pelo enxofre, a redução só pode ocorrer na superfície do óxido de ferro.
O enxofre como praga redutora também é a causa do inchaço excessivo dos grânulos descritos acima. Como o ferro só pode se cristalizar na direção do óxido de ferro em decomposição, os cristais de ferro se desenvolvem de maneira alongada e fibrosa. A estrutura do pellet já afrouxada devido ao primeiro estágio de redução é reforçada novamente e o volume do pellet pode crescer até duas a três vezes o seu volume original.
Para manter a proporção de compostos de enxofre o mais baixa possível, os minérios sulfídicos são convertidos em óxidos por meio de uma torrefação cuidadosa e são introduzidos aditivos que ligam o enxofre.
Reações químicas durante a redução
No alto-forno, às vezes ocorrem vários processos metalúrgicos ao mesmo tempo, nos quais, por um lado, o minério de ferro é reduzido a ferro-gusa em várias etapas e os componentes não redutíveis são transferidos para a escória.
Para iniciar uma redução no minério de ferro em primeiro lugar, no entanto, os gases redutores necessários devem ser gerados primeiro. Isso ocorre na área inferior do alto-forno, quando o carbono contido no coque é queimado com oxigênio .
A reação é fortemente exotérmica , o que significa que o calor é liberado, que é de 394,4 kJ / mol nesta reação e o alto-forno na área dos bicos do anel de sopro quente a uma temperatura de 1800 a 2000 ° C, com o uso de oxigênio adicional, mesmo aquecido a 2200 ° C. No entanto, duas imediatamente após as reações endotérmicas , isto é, as reações que consomem calor baixam a temperatura novamente para cerca de 1600 a 1800 ° C.
A chamada “ reação de Boudouard ” , que, no entanto, requer uma temperatura mínima de 1000 ° C, requer 172,45 kJ / mol.
Uma divisão simultânea do vapor no gás quente requer outro 131,4 kJ / mol.
Os dois gases que podem ser reduzidos, monóxido de carbono e hidrogênio, aumentam contra o fluxo de material no alto-forno. Devido a esta propriedade - afundamento da coluna de coque Möller por um lado e aumento dos gases de reação fluindo contra o material a granel em movimento, por outro - o alto-forno também é referido como um "reator de contracorrente" e um "reator de leito móvel".
A chamada “redução indireta” ocorre na zona de temperatura entre 400 e 900 ° C. Os vários óxidos de ferro reagem com o monóxido de carbono ou hidrogênio em três estágios, até que finalmente o ferro metálico esteja presente:
Reação com monóxido de carbono (CO) | Reação com hidrogênio (H 2 ) |
---|---|
A magnetita mais ferrosa é formada a partir da hematita . | |
De magnetita produzida wustita . | |
O ferro metálico é produzido a partir da wüstita, que é coletada no alto-forno abaixo. |
Enquanto o dióxido de carbono (CO 2 ) resultante permanecer na faixa de temperatura acima de 1000 ° C, ele é repetidamente regenerado em monóxido de carbono (CO) pela reação de Boudouard e fica novamente disponível para o processo de redução. A redução por hidrogênio é particularmente eficaz em torno de 800 ° C. Um conteúdo de apenas 10% de hidrogênio no gás de reação triplica a taxa de redução, mas diminui novamente quando a temperatura aumenta ainda mais. O tamanho do grão do minério também não deve ultrapassar um determinado nível, para que os caminhos de difusão do hidrogênio não se tornem muito grandes.
Na faixa de temperatura de 900 a 1600 ° C, também ocorre uma "redução direta" com carbono:
Os companheiros de ferro manganês , silício e fósforo também são incluídos no processo e reduzidos, por meio do qual o calor é consumido:
Ao mesmo tempo, o ferro já reduzido na zona de carbonização absorve carbono em torno de 1100 a 1200 ° C, diretamente do coque incandescente ou do monóxido de carbono gasoso.
A absorção de carbono diminui o ponto de fusão de 1538 ° C ( ferro puro ) para cerca de 1300 a 1400 ° C (ponto de fusão da mistura eutética , o ledeburita , com 4,3% em peso C: 1147 ° C).
Monitoramento e regulação do processo de alto-forno
No curso da automação e garantia de qualidade para manter a competitividade, por um lado, e os crescentes requisitos de segurança para a proteção de pessoas e máquinas, por outro, vários dispositivos de medição e controle são inevitáveis. O processo de fundição está naturalmente sujeito a maiores ou menores flutuações, pois a composição do Möller, coque e jateamento a quente, incluindo os aditivos injetados, também variam dentro dos limites de tolerância . O curso e a velocidade da reação flutuam de acordo, o que levaria a sérias interrupções sem monitoramento e medidas de contra-regulação adequadas.
Variáveis medidas importantes são acima de tudo:
na quantidade de gota |
|
do poço ao saco de carvão |
|
ao nível do suprimento de ar quente |
|
na base da moldura |
|
Além disso, sondas horizontais também são usadas para medir a espessura das camadas de Möll, bem como a pressão e a velocidade do gás que passa pela coluna de Möller. Para proteger contra falhas, alguns dispositivos de medição, como aqueles para medir a profundidade da superfície de carga , são redundantes.
Perturbações no processo de alto-forno
Carregando pendurado
Devido à desintegração do Möller e do coque durante a redução, a coluna de Möller no eixo pode se compactar e, eventualmente, voltar a subir. Uma coluna Möll pendurada desta forma é inicialmente perceptível no sentido de que a medição de profundidade não registra mais nenhum movimento de afundamento na superfície de carga, mas a pressão e a temperatura do gás de topo também caem porque é difícil passar pelas fendas cada vez mais estreitas no coluna Möll compactada. A pressão do vento, por outro lado, aumenta à medida que encontra maior resistência.
Abaixo da zona de suspensão, no entanto, o processo de redução e derretimento continua inabalável até que uma cavidade seja finalmente formada entre o Möller suspenso e afundando. Uma vez que, por um lado, há o risco de uma coluna Möller colapsar repentinamente na cavidade, levando a sérias interrupções do processo e danos ao alto-forno e, por outro lado, o ferro-gusa e a escória ameaçam subir para os moldes de sopro, uma reação ao As alterações nas características mencionadas nos resultados da medição devem ocorrer o mais cedo possível. Isso inclui, por exemplo, o chamado "transtorno", um estrangulamento forte único ou, se necessário, repetido, da quantidade de vento e, portanto, a contrapressão na coluna Möll, que o força a deslizar devido ao seu próprio peso.
Formação de abordagem
A aglomeração de Möller e coque nas paredes internas do alto-forno pode ter várias causas. Com o tempo, o perfil da armadura muda devido à abrasão física e química , o que pode resultar em condições de fixação mais fáceis nos locais. Como resultado, os elementos de resfriamento salientes também facilitam a formação de depósitos. A própria composição da argamassa também influencia o processo de endurecimento, visto que, entre outras coisas, uma escória de base tem uma proporção correspondentemente maior de diferentes álcalis , que atuam como auxiliares de endurecimento, para uma melhor ligação do enxofre . Lotes menores dificilmente são perceptíveis no início, mas podem crescer muito rapidamente e levar a mau funcionamento no processo de alto-forno; especialmente se estes se rompem repentinamente e causam irregularidades na composição da Möllersäule.
Abordagens maiores podem ser medidas estreitando a seção transversal do forno e, assim, aumentando a velocidade do fluxo do vento, que arrasta mais partículas de poeira. Além do aumento da emissão de poeira, a formação de depósitos também pode promover os fenômenos de suspensão mencionados acima. Além disso, o resultado são flutuações no ciclo do forno e na qualidade do ferro-gusa devido aos depósitos de desintegração. Finalmente, o acúmulo de elementos de resfriamento protuberantes também pode causar danos a eles.
Graças aos sensores de pressão e temperatura nas paredes do forno e sondas de medição que podem ser empurradas horizontalmente para a coluna Möll, as mudanças na seção transversal e, portanto, as abordagens podem agora ser localizadas de forma mais rápida e precisa. Mudanças apropriadas na roupa de cama geralmente podem eliminá-los. No passado, altos-fornos maiores, em particular, tinham que ser derrubados primeiro e, em seguida, as abordagens perfuradas ou explodidas.
A entrada de água
A entrada de água através de elementos de resfriamento danificados pode levar a interrupções consideráveis no processo de alto-forno, uma vez que com grandes quantidades a evaporação da água acarreta uma grande perda de energia térmica e os vários processos de redução param. A entrada de água pode ser medida, por um lado, pelo aumento do conteúdo de hidrogênio no gás de topo e, por outro lado, pelo aumento do consumo de água de alimentação , que supostamente compensa a perda de água em circuitos de resfriamento fechados.
A subdivisão e conexão sensata dos elementos e linhas de resfriamento uns com os outros em zonas horizontais ou "discos de resfriamento" permite que os elementos danificados sejam descobertos e substituídos mais rapidamente e as perdas de água sejam reduzidas ao mínimo. Em sistemas de refrigeração abertos, por outro lado, um teste de pressão é necessário em cada elemento de refrigeração.
Desligar
Diferentes procedimentos são necessários, dependendo se a siderurgia deseja desligar o alto-forno apenas brevemente (vaporização) ou desligá-lo completamente e desligá-lo (soprando) .
Fumegante
Se um alto-forno tiver que ser desligado apenas temporariamente, por exemplo, no caso de gargalos no fornecimento ou pequenos reparos, ele é amortecido . Ao fazer isso, o carregamento é primeiro comutado, dependendo da duração planejada da interrupção da operação. Agora consiste, por um lado, em um lubrificador a vapor “leve”, o que significa menos ferro, e, por outro lado, em um número maior de camadas de coque. Durante a última vazamento antes da parada, deve-se tomar cuidado para garantir que o ferro-gusa e a escória sejam drenados o mais completamente possível. Se a fase de vaporização deve durar mais, a porca de forno também é usada. Quando o forno está parado, todas as linhas de fornecimento e descarga são fechadas, os bicos de ar quente são bloqueados e a superfície de carga é coberta com minério fino ou areia de escória para que o forno possa manter seu calor pelo maior tempo possível e o a tiragem natural não leva a queimaduras desnecessárias de coque. Para evitar a entrada de água, o que levaria a graves interrupções no processo do alto-forno, o sistema de resfriamento só é desligado após um cuidadoso teste de vazamento.
O novo sopro após fases de amortecimento mais longas ocorre na ordem inversa das etapas de trabalho individuais durante o cozimento a vapor, embora inicialmente apenas algumas ventaneiras do sistema de sopro quente na área do furo de torneira, então outros bicos são gradualmente colocados em operação. Se necessário, o orifício da agulha também é ajustado mais alto por algum tempo.
Soprar
Se a operação normal não for mais possível, entre outras coisas porque o revestimento está tão gasto que precisa ser substituído, o alto-forno é "queimado".
O processo de alto-forno continua inicialmente na área inferior, mas a alimentação de alimentação é desligada e o suprimento de vento é bastante reduzido na fase inicial e, finalmente, também desligado. Na fase de sopro profundo (rebaixamento da coluna de coque-Möller), o vapor d'água é injetado através de bicos especiais em todos os pontos onde “mortos”, ou seja, espaços vazios são formados. Às vezes, a água também é adicionada de cima. Isso evita a formação de misturas explosivas de gás e ar. Espaços mortos surgem acima de tudo acima da superfície de carga até a ventilação superior, mas também nos espaços entre a eclusa de gás superior, dependendo da posição das válvulas de corte na ventilação de gás entre o forno e o saco de pó ou no pó saco em si, bem como nos vórtices e na válvula do forno. Outro método para evitar explosões de gás é queimar os gases do forno que escapam da superfície de carga com o auxílio de uma lança de ignição de gás de coque em combustão contínua. A finalização do processo de sopro é o vazamento da porca do forno , onde, além da escória, dependendo da duração da viagem do alto-forno e das condições de resfriamento na cremalheira, várias toneladas de ferro-gusa podem se acumular.
No final da jornada do forno, todo o revestimento do tijolo refratário é geralmente renovado e os componentes de aço danificados substituídos. Freqüentemente, o tempo de inatividade do forno também é usado para substituir equipamentos tecnicamente desatualizados, como dispositivos de medição e análise, por novos. Além de melhorar a qualidade dos produtos do alto-forno, isso também ajuda a reduzir o consumo de energia e a poluição ambiental.
Geralmente, leva vários meses para que todos os componentes danificados ou desatualizados sejam substituídos. No entanto, se os componentes restantes forem de boa qualidade, um alto-forno pode sobreviver a várias viagens de forno até que seja finalmente desligado. Em março de 2008, por exemplo, o “Grande alto-forno 1” em Duisburg-Schwelgern iniciou sua quinta turnê de fornalha.
Produtos de alto-forno
Ferro gusa
O objetivo de um processo de alto-forno perfeitamente ajustado é a produção de ferro-gusa da mais alta qualidade possível, que tenha o mínimo de matéria estranha possível e não tenha absorvido muito carbono.
De acordo com a DIN EN 10001 , o ferro-gusa é definido como uma liga de ferro com mais de 2% de carbono e alguns outros elementos com as seguintes proporções máximas: manganês ≤ 30%, silício ≤ 8%, fósforo ≤ 3% e cromo ≤ 10 % A proporção de outras misturas não deve exceder 10%. Para fins de garantia de qualidade , uma amostra é retirada para uma análise química a cada torneira.
Os chamados “gusa branco” (também de aço de ferro-gusa ) é produzida em 9 dos 10 altos-fornos plantas, em que o carbono contido se encontra sob a forma de carboneto de ferro ou manganês carboneto e superfície de fractura tem um brilhante, prata -branco brilho . O ferro branco está geralmente diretamente na forma líquida usando um carro torpedo fechado para o aço transportado nas proximidades, mas também pode ser fundido lingotes ou grânulos de ferro (tamanho de grão ≈ 2-16 mm). O ferro-gusa branco é usado como matéria-prima para a produção de aço e é liberado de suas substâncias indesejáveis e de uma grande parte do carbono em uma usina de aço soprado (“caldeira de aço”) por sopro de oxigênio. Estes deixam o aço acabado brilhante como gases (dióxido de enxofre, dióxido de carbono) ou com os aditivos como escória (silicatos ou fosfatos de cálcio e manganês).
O pequeno restante da siderurgia produz principalmente "ferro-gusa cinza" (também ferro de fundição ), no qual o carbono se cristaliza não ligado como grafite e a superfície da fratura mostra um cinza fosco mais escuro. O ferro-gusa cinzento é utilizado como matéria-prima para a produção de diversos tipos de ferro fundido, como ferro fundido cinzento com grafite lamelar ou grafite esferoidal , ferro fundido maleável e aço fundido . Algumas empresas também se especializaram em tipos especiais de ferro- gusa , como ferromanganês (ferro frito) ou ferrossilício .
escória
A escória produzida durante o processo de alto-forno consiste em cerca de 38-41% de óxido de cálcio (CaO), 7-10% de óxido de magnésio (MgO), 34-36% de sílica (SiO 2 ), 10-12% de alumina (Al 2 O 3 ), 1, 0-1,5% de enxofre (S), 1,0% de dióxido de titânio (TiO 2 ), 0,16-0,2% de óxido de ferro ( FeO ) e vários outros óxidos e sulfetos.
Fundidores experientes freqüentemente veem a escória ainda líquida para ver qual composição e propriedades aproximadas ela contém. Um simples "teste de gancho", em que um gancho de ferro é mergulhado na escória, geralmente é suficiente para testar o mesmo. Se a escória permanecer no gancho em gotas curtas e difíceis ao ser levantada (escória curta) , ela é " básica " com uma relação de peso de CaO: SiO 2 > 1,0. Se, por outro lado, a escória escorre do gancho em fios longos (escória longa) , é "ácida" com uma relação CaO: SiO 2 <1,0.
Enquanto a escória de alto-forno ainda tinha a tarefa de absorver a ganga dos minérios e as cinzas do coque, a dessulfuração do ferro gusa e que serve como uma parede de protecção na moldura contra a radiação de calor, depois de tocar, dependendo da sua composição e propriedades, torna-se uma matéria-prima valiosa para vários fins continuaram a ser usados. Além de gerar escória de alto-forno , tijolos ou bordas de escória e lã de escória , também é processado lastro rodoviário e ferroviário , blocos de ar , cimento Portland e cimento de alto-forno .
Gás de fornalha

O gás de topo que sai do topo do alto-forno a uma temperatura de 150 a 200 ° C consiste em 22-24% de dióxido de carbono (CO 2 ), 18-21% de monóxido de carbono (CO), 52-59% de nitrogênio (N 2 ), 1-3% de hidrogênio (H 2 ), bem como de vapor de água e vestígios de metano . Além de seu uso principal como fornecedor de combustível para acionar os aquecedores eólicos, também é usado, entre outras coisas, como gás de aquecimento em laminadores , caldeiras a vapor , câmaras de coque e sistemas de aquecimento urbano , bem como combustível para motores a gás .
Devido a muitas medidas para melhor utilização do minério e do gás e, ao mesmo tempo, redução do consumo de coque, a quantidade total de gás de alto forno produzida e seu valor calorífico caíram com o tempo. Desde a década de 1990, cerca de 1.500 a 2.000 m³ de gás de forno com valor calorífico entre 3.150 e 3.570 kJ / m³ foram produzidos por tonelada de ferro-gusa . Com a adição de coque ou gás natural , esse valor aumenta para cerca de 4.500 kJ / m³. Além disso, existem cerca de 25 kg de pó de alto-forno por tonelada de ferro-gusa, o que corresponde a um teor de pó no gás de alto-forno de cerca de 20–30 g / m³.
A fim de proteger os queimadores, motores a gás e turbinas operadas pelo gás de forno de danos por abrasão , mas também por razões de proteção ambiental , o gás de forno foi despojado e limpo desde o início do século XX . As turbinas a gás de alto-forno desde a década de 1970 exigem z. B. gás de alta pureza com um teor de poeira de no máximo 0,5-1 mg / m³.
A limpeza ocorre em várias etapas, desde a limpeza a seco com o auxílio de sacos de pó e turbilhonadores até a limpeza úmida em lavadores de gases e desintegradores até a limpeza fina com o auxílio de sistemas de mangas ou filtros de mangas e filtros eletrostáticos . O gás limpo que pode então ser usado ainda contém um teor de poeira de 0,006 a 0,03 g / m³.
Desempenho e consumo
Até 1914, um alto-forno fornecia cerca de 300 a 400 toneladas de ferro-gusa por dia e entre 1950 e 1960 já era capaz de produzir 2.500 toneladas por dia.
Na década de 1970, os melhores fornos do mundo entregavam 60 toneladas por metro quadrado de superfície da cremalheira e mais por dia, com um consumo médio de coque e óleo em torno de 503 quilos por tonelada de ferro-gusa. Para altos-fornos de médio porte com um diâmetro de carcaça de 10 a 11 metros, isso corresponde a uma produção diária de 5.000 a 6.000 toneladas.
Em 1980, o consumo específico de coque de um alto-forno na República Federal da Alemanha era de cerca de 515 quilos por tonelada de ferro-gusa. O consumo específico de óleo para aquecimento foi de 23 quilos por tonelada de ferro-gusa. Em 1994, o consumo de coque caiu para cerca de 379 quilos, enquanto o consumo de óleo para aquecimento aumentou para cerca de 45 quilos por tonelada. Desde 1985, o carvão tem sido cada vez mais usado como agente redutor em vez de coque processado.
Grandes altos-fornos como o "Alto-forno 5" do alto-forno Rogesa nas instalações da fábrica Dillinger Hütte com um diâmetro de estrutura de 12 metros produzem cerca de 7.000 toneladas por dia. Altos-fornos maiores podem produzir até 12.000 toneladas de ferro-gusa por dia.
Em 1950, a produção global anual era de cerca de 189 milhões de toneladas de ferro-gusa, mas aumentou para cerca de 1808 milhões de toneladas no final de 2018. O "Alto-forno 2" da ThyssenKrupp Steel em Schwelgern , que começou a operar no final de 1993 , tinha um diâmetro de quadro de 14,9 metros e uma produção diária de mais de 10.000 toneladas de ferro-gusa.
Em 2007, grandes altos-fornos com um diâmetro de carcaça de cerca de 15 metros produziram uma média de cerca de 12.000 toneladas de ferro-gusa por dia, o que corresponde a uma produção anual de cerca de 4 milhões de toneladas. Para isso, são necessários cerca de 19.200 toneladas de minério de ferro, 4.000 toneladas de coque, 1.750 toneladas de carvão injetado (pó de carvão a ser injetado pelos bicos de ar quente) e 11 milhões de metros cúbicos de ar por dia. Isso corresponde a um consumo de cerca de 1.600 quilos de minério, 330 quilos de coque, 146 quilos de carvão injetado e 917 metros cúbicos de ar por tonelada de ferro-gusa. Os subprodutos produziram 3300 toneladas de escória e 17 milhões de metros cúbicos de gás de forno por dia. Cerca de uma tonelada de coque é usada para derreter a escória para cada 3,2 toneladas de escória.
Veja também
Fontes e Referências
literatura
Compra direta do alto-forno
- Manfred Rasch (ed.): O forno de coque de 1709 até o presente. 2ª Edição. Klartext Verlag , Essen 2015.
- Hans Schoppa: O que o operador de alto-forno precisa saber sobre seu trabalho . 4ª edição. Verlag Stahleisen, Düsseldorf 1992, ISBN 3-514-00443-9 .
- Gerhard Winzer, Eberhard Reichenstein: Desenvolvimento da tecnologia de alto-forno . Relatórios realizados no Estudo de Contato “Metalurgia do Ferro; Parte I: Fabricação de ferro ”. Em: F. Oeters, R. Steffen (Ed.): Metallurgie . fita 2 . Verlag Stahleisen, Düsseldorf 1982, ISBN 3-514-00260-6 , p. 79-84 .
- H. Dickmann: Desenvolvimento do aquecimento eólico de alto-forno até a invenção de EA Cowpers . In: Brohltal AG para a indústria de pedra e argila (ed.): Cem anos de aquecimento do vento Cowper . Burgbrohl (distrito de Koblenz) 1958.
- MA Pavlov (М. А. Павлов): Projeto e cálculo de altos-fornos . In: Metalurgia do ferro-gusa . 2ª Edição. fita 3 . VEB Verlag Technik, Berlin 1953, DNB 453723004 , número de licença Dg.-No. 370/39/53 (DDR) - (Russo: Металлургия Чугуна, Часть третья: Доменная печь . Traduzido por Erich Marquardt).
Processo de alto-forno
- K. Grebe: O comportamento do alto-forno de Möller e coque . Relatórios realizados no Estudo de Contato “Metalurgia do Ferro; Parte I: Fabricação de ferro ”. Em: F. Oeters, R. Steffen (Ed.): Metallurgie . fita 2 . Verlag Stahleisen, Düsseldorf 1982, ISBN 3-514-00260-6 , p. 85-145 .
- MA Pavlov (М. А. Павлов): O processo do alto-forno . In: Metalurgia do ferro-gusa . 2ª Edição. fita 2 . VEB Verlag Technik, Berlin 1953, DNB 367559374 , número de licença Dg.-No. 370/40/53 (GDR) - (Russo: Металлургия Чугуна, Часть вторая: Доменный Процесс . Traduzido por Rudolf Rickert, Walter Philipp, Alexander Junge, Heinz Frahn).
- Association of German Ironworkers (Ed.): O processo do alto-forno - O modelo de simulação cinético-dinâmico . Relatório de trabalho conjunto com contribuições da conferência “Modelos Matemáticos do Processo do Alto Forno” nos dias 2 e 3 de dezembro de 1971 em Düsseldorf. Verlag Stahleisen, Düsseldorf 1973, ISBN 3-514-00124-3 .
- Richard Troska: As dimensões do forno com base no processo do forno. Weimar 1867 ( disponível online na pesquisa de livros do Google; último acesso em 27 de maio de 2012)
Em geral
- Jürgen Ruge, Helmut Wohlfahrt: Tecnologia de materiais . 8ª edição. Springer Verlag, 2007, ISBN 3-8348-0286-7 .
- Karl Taube: compacto de produção de aço: fundamentos da metalurgia do ferro e do aço . Vieweg Technik, Braunschweig / Wiesbaden 1998, ISBN 3-528-03863-2 , p. 60–159: alto-forno .
- Parte I: Fabricação de ferro . Relatórios realizados no Estudo de Contato “Metalurgia do Ferro”. Em: F. Oeters, R. Steffen (Ed.): Metallurgie . fita 2 . Verlag Stahleisen, Düsseldorf 1982, ISBN 3-514-00260-6 .
- Association of German Ironworking People (Ed.): Representação comum da indústria siderúrgica . 17ª edição. Verlag Stahleisen, Düsseldorf 1970.
- Fritz Toussaint: O caminho do ferro . 6ª edição. Verlag Stahleisen, Düsseldorf 1969.
- Otto Johannsen (em nome da Associação dos Metalúrgicos Alemães): História do ferro . 3. Edição. Verlag Stahleisen, Düsseldorf 1953.
- Robert Durrer : Noções básicas de produção de ferro . Verlag Francke, Bern 1947, p. 56-58 .
- Johann Christian zu Solms-Baruth, Johann Heinrich Gottlob von Justi: Tratado dos martelos de ferro e altos fornos na Alemanha. Rüdiger, Berlin / Stettin / Leipzig 1764. (E-Book: Becker, Potsdam 2010, ISBN 978-3-941919-73-0 )
- AF Holleman , E. Wiberg , N. Wiberg : Textbook of Inorganic Chemistry . 102ª edição. Walter de Gruyter, Berlin 2007, ISBN 978-3-11-017770-1 .
- Peter Atkins : Physical Chemistry . 2ª Edição. Wiley-VCH, Weinheim 1996, ISBN 3-527-31546-2 .
Links da web
- Fotos de todos os métodos de produção de ferro e aço e processamento posterior
- Do minério de ferro ao ferro-gusa: a estrutura do alto-forno
- Museu do alto-forno Radwerk IV em Vordernberg
- Jun-Ichi Kokado: O desenvolvimento técnico da indústria siderúrgica japonesa ( Memento de 17 de janeiro de 2008 no Internet Archive )
Evidência individual
- ↑ Hohofen . In: Heinrich August Pierer , Julius Löbe (Hrsg.): Enciclopédia universal do presente e do passado . 4ª edição. fita 8 . Altenburg 1859, p. 472 ( zeno.org ).
- ↑ Wirtschaftsvereinigung Stahl (Ed.): Fatos sobre a indústria siderúrgica na Alemanha 2020 . ( stahl-online.de [PDF; 3.4 MB ; acessado em 15 de março de 2021]).
- ↑ a b Johannsen: History of Iron , pp. 9-11.
- ↑ Matthias Zwissler, Roman Landes: Investigações em produtos de fogo de corrida , simpósio da IGDF International Society for Damascus Steel Research eV em Polle, 20 de agosto de 2005 ( investigações em produtos de fogo de corrida PDF; 3,54 MB).
- ↑ Johannsen: History of Iron , p. 11, 121.
- ↑ Johannsen: History of Iron , pp. 121-122.
- ↑ Albrecht Jockenhövel: O caminho para o alto-forno - A época das cabanas de massa medievais e do início da modernidade. In: Eisenland, nas raízes da indústria siderúrgica de Nassau. Ed. Associação para a antiguidade e pesquisa histórica de Nassau e. V., Taunusstein 1995, ISBN 3-922027-88-1 , pp. 83-98.
- ↑ a b c Durrer: Fundamentals of iron production , pp. 56–58.
- ↑ Johannsen: History of Iron , página 133.
- ^ Meyers Konversationslexikon - Blauofen
- ↑ Descrição geral da indústria siderúrgica , página 7.
- ^ Ludwig Beck : Contribuições para a história da indústria do ferro em Nassau. In: Nassau Annals. Volume 33 (1902/03), página 212.
- ↑ Michael Gechter: Arqueologia da mineração na Terra de Bergisches. In: gv-roesrath.de. History Association Rösrath eV, acessado em 18 de abril de 2019 .
- ↑ Aufbruch ins revier , Hoesch 1871–1961, página 34
- ↑ Aufbruch ins revier , Hoesch 1871–1961, página 43
- ↑ Johannsen: History of Iron , página 296.
- ↑ a b Descrição comum da indústria de ferro e aço , pp. 8–9.
- ↑ Harald Pöcher: Guerras e batalhas no Japão, que fizeram história: dos primórdios a 1853. LIT Verlag, Münster 2009, p. 34 visualização limitada na pesquisa de livros do Google
- ↑ Johannsen: History of Iron , pp. 22-23.
- ↑ Johannsen: History of Iron , página 35.
- ↑ Peter Dahlmann, Gerhard Endemann, Hans Jürgen Kerkhoff, Hans Bodo Lüngen: Maneiras de aumentar a eficiência na indústria do aço , Steel Institute VDEh. Wirtschaftsvereinigung Stahl, setembro de 2010 ( Maneiras de aumentar a eficiência na indústria do aço PDF 1.7 MB, p. 6 ( Memento de 17 de dezembro de 2015 no Arquivo da Internet ))
- ↑ a b Construção do alto-forno 8 em Duisburg-Hamborn da ThyssenKrupp Steel AG
- ↑ Schoppa: Was der Hochöfner… , pp. 52–53.
- ^ Taube: compacto de produção de aço , página 92.
- ↑ Johannsen: Geschichte des Eisens , pp. 371–372.
- ↑ a b Roger Kneip: DA HISTÓRIA DA INDÚSTRIA DO AÇO - Mais de 25 anos de combate à gota sem sinos
- ↑ Schoppa: Was der Hochöfner… , pp. 55–56.
- ↑ Descrição geral da indústria siderúrgica , página 59.
- ↑ Schoppa: Was der Hochöfner… , pp. 38–39.
- ↑ Taube: compacto de produção de aço , pp. 62–63.
- ↑ a b Dez anos de alto-forno Schwelgern 2 e 38 milhões de toneladas de ferro-gusa ( Memento de 29 de novembro de 2011 no Arquivo da Internet )
- ↑ ThyssenKrupp: Primeiro ciclo do forno terminou após 21 anos: o maior alto-forno da Europa está sendo modernizado. Comunicado de imprensa de 16 de maio de 2014.
- ↑ Vaclav Smil: Ainda a Idade do Ferro. Ferro e aço no mundo moderno. , Butterworth-Heinemann (Elsevier), Oxford Cambridge 2016, página 90. ISBN 978-0-12-804233-5 . Trecho , acessado em 29 de setembro de 2016.
- ^ Três dos 10 maiores caldeirões mundiais de propriedade da coreana POSCO. In: Arirang News. 24 de agosto de 2013, com vídeo (0:37 min.)
- ↑ Aços planos - entrega de estrutura no alto-forno B concluída sem acidentes ( lembrança de 19 de setembro de 2015 no Arquivo da Internet )
- ↑ Descrição geral da indústria siderúrgica , página 101.
- ↑ a b stahl-online.de - Produção de ferro-gusa e aço ( Memento de 15 de janeiro de 2012 no Arquivo da Internet ) (De acordo com a produção de ferro-gusa e aço ( Memento de 10 de fevereiro de 2011 no Arquivo da Internet ), valores ter sido inalterada desde outubro de 2007 website)
- ↑ a b Descrição comum da indústria siderúrgica , página 61.
- ↑ HW Gudenau, H. Kainer, G. Pitzko, M. Scheiwe: Comportamento termo-mecânico de revestimentos de estrutura de alto-forno. In: Aço e Ferro. 111 (1991) 9, pp. 71-81, 188.
- ↑ Schoppa: Was der Hochöfner… , pp. 43–44.
- ↑ Taube: Steel Production Compact , pp. 71–73.
- ↑ Taube: compacto de produção de aço , pp. 84–85.
- ↑ Dickmann: Desenvolvimento do aquecimento eólico do alto-forno ... , p. 1.
- ↑ Johannsen: History of Iron , página 325.
- ↑ Johannsen: History of Iron , página 327.
- ↑ Dickmann: Desenvolvimento do aquecimento eólico do alto-forno ... , p. 4.
- ↑ Dickmann: Desenvolvimento do aquecimento eólico do alto-forno ... , p. 6.
- ↑ Dickmann: Desenvolvimento do aquecimento eólico de alto-forno ... , p. 9.
- ↑ Schoppa: Was der Hochöfner ... , página 58.
- ^ Taube: Produção de aço compacta , página 47.
- ^ Taube: Produção de aço compacta , página 46.
- ^ Taube: compacto de produção de aço , página 59.
- ↑ a b Winzer, Reichenstein: Desenvolvimento de tecnologia de alto-forno , pp. 80-81.
- ↑ Relatório de inovação: Alto-forno: pelotas de plástico em vez de coque e óleo pesado
- ↑ Ao usar plásticos antigos, a voestalpine reduz as emissões de CO 2 em Linz em mais de 400.000 toneladas por ano. (PDF 32 kB) In: voestalpine.com. voestalpine AG, 16 de junho de 2007, acessado em 17 de julho de 2019 .
- ↑ a b Ruge, Wohlfahrt: Technologie der Werkstoffe , página 195.
- ↑ Schoppa: Was der Hochöfner ... , página 49.
- ↑ a b Taube: Produção de aço compacto , pp. 152–154.
- ↑ Schoppa: Was der Hochöfner ... , página 51.
- ↑ a b c d Schoppa: Was der Hochöfner… , pp. 85–88.
- ^ Toussaint: Der Weg des Eisens , página 65.
- ^ Grebe: O comportamento do alto-forno de Möller e Koks , pp. 95-101.
- ^ Grebe: O comportamento do alto-forno de Möller e Koks , pp. 101-109.
- ↑ Winzer, Reichenstein: Desenvolvimento de tecnologia de alto-forno , página 79.
- ^ Grebe: O comportamento do alto-forno de Möller e Koks , pp. 91-92.
- ^ Grebe: O comportamento do alto-forno de Möller e Koks , pp. 104-107.
- ↑ Atkins: Physical Chemistry , página 1108.
- ^ AF Holleman , E. Wiberg , N. Wiberg : Textbook of Inorganic Chemistry . 102ª edição. Walter de Gruyter, Berlin 2007, ISBN 978-3-11-017770-1 , página 897.
- ↑ a b c Taube: produção de aço compacto , página 131.
- ↑ Schoppa: Was der Hochöfner ... , pp. 64-66.
- ↑ Taube: Steel Production Compact , pp. 118–124.
- ↑ Schoppa: Was der Hochöfner ... , p. 88.
- ↑ Taube: Produção de aço compacto , página 147.
- ↑ Schoppa: Was der Hochöfner… , pp. 89–90.
- ↑ Taube: Steel Production Compact , pp. 146–147.
- ↑ Schoppa: Was der Hochöfner ... , p. 90.
- ^ Taube: Produção de aço compacta , página 148.
- ↑ ThyssenKrupp: A quinta jornada do forno pode começar: Grande alto-forno 1 em Duisburg-Schwelgen é soprado novamente no início de abril após a modernização ; Comunicado de imprensa de 19 de março de 2008, 11h00
- ↑ a b Descrição comum da indústria de ferro e aço , pp. 78–79.
- ↑ a b Taube: Produção de aço compacto , pp. 158–159.
- ↑ Descrição geral da indústria siderúrgica , pp. 83–84.
- ^ A b Karl-Heinz Schmidt, Ingo Romey, Fritz Mensch: Carvão, petróleo, gás natural: química e tecnologia. Vogel Verlag, Würzburg 1981, ISBN 3-8023-0684-8 .
- ^ Taube: compacto de produção de aço , página 159.
- ↑ Schoppa: Was der Hochöfner ... , p. 102.
- ↑ Descrição geral da indústria siderúrgica , página 96.
- ↑ Schoppa: Was der Hochöfner ... , página 63.
- ↑ Bergbau-Lexikon der steinkohle-portal.de - alto-forno ( Memento de 30 de março de 2012 no Arquivo da Internet )
- ↑ Sobre a proteção do clima em stahl-online.de: O aço é indispensável para um mundo com baixas emissões.
- ↑ World Steel Association: World Steel in Figures 2019 . (PDF 1.9 MB) 6 de junho de 2019, p. 6 , acessado em 17 de julho de 2019 .